Read through the following experiments in preparation to execute in class. Answer the following questions.
1. There are four types of natural glass described below. What do the four types have in common with regards to their formation?
2. Why is quartz not considered a type of natural glass?
3. What are the independent and dependent variables for each Experiments A, B, and C?
4. What are some of the controls that had to be maintained in each of the Experiments A, B, and C?
Natural verses Fabricated Glass
Types of Natural Glass
Fulgurite – Glass resulting from a strike in a mass of sand that has the right combination of minerals. This forms brittle, glassy tubes that preserve the shape of the lightening as it travels through sand.
Quartz – This glass-like rock crystal has the transparency of glass, but its crystalline structure prevents it from fully fitting the definition of glass.
1 A simplified definition of glass describes it as a material that solidifies from a molten state without forming crystals.
Obsidian – Glass formed due to the intense heat of a volcano.

Tektite – Glass that forms as molten blobs of earth are tossed into the air when a meteorite hits the earth.
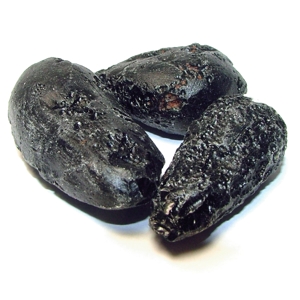
Euplectella – A glass sponge found in the western Pacific Ocean near the Phillipines with a hollow-cylindrical skeleton made from silica.
Glass occurs in nature when sand or stone endures extreme heat and then cools rapidly. Man used natural glass to create tools and jewelry, but was not able to fully take advantage of the beneficial properties of glass till he could make it himself. After witnessing how glass formed in nature, man began to modify glass recipes that create the many glass objects we depend on everyday.
Fabricating Glass
The glass that surrounds us in our every day lives, from bottles to windows, is commonly made from silica (silicon dioxide, SiO2), also known as sand. When silica is cooled from a molten state it begins to behave like a solid, though it technically retains its status as a liquid. The structure of the molecules of glass does not change as it goes from a hot liquid state to a cold rigid one. The temperature at which silica begins to act like a solid, known as the transition temperature, is relatively high. Pure silica creates a very strong glass with great chemical durability, but the cost of manufacturing a glass that requires such a high melting temperature prevents its commercial use. The solution for this problem can be found in the addition of modifiers known as flux. Fluxing agents, such as alkali or alkaline earth oxides, lower the temperature at which the pure silica melts by disrupting the network connectivity. As modifiers lower the transition temperature, they also decrease the chemical durability and make the formation of glass more difficult. This requires a glass engineer to balance cost and quality when creating a recipe that best fits the needs of the glass manufacturer.
Understanding Fabrication through Candy Making
The methods used for making candy demonstrate many of the same principles as in the formation of glass. Sugar replaces silica as the glass former and the use of water mimics alkali as a modifier. Sugar (sucrose) has a melting temperature of 186 ºC while water has a melting temperature of 0ºC. Comparably, silicon dioxide has a melting temperature of 1723ºC while alkali has a melting temperature of 1275ºC. The experiments below use a) sugar alone, b) sugar and water, c) sugar, corn syrup and water.
Vocabulary
Transition temperature
Flux
Fiber draw
Viscosity
Objective
After this experiment, the student should be able to understand these basic principles of glass science and technology:
1. If a pure melt is cooled slowly enough, it forms a single crystal, while cooling quickly produces a polycrystalline solid. Crystal formation can be completely suppressed if the cooling rate is sufficiently increased, thus creating glass.
2. Impurities, mechanical agitation, bubbles and other factors can create crystals. The addition of a modifier decreases the ability of the melt to form glass.
3. The number of ingredients may improve the ability of a melt to form glass.
4. Modifiers overall weaken the glass.
5. The viscosity of a melt can be controlled by varying the temperature, which makes it possible to control the drawing of glass fibers.
Materials
Hotplate or electric stovetop
1 one-quart stainless steel pan
12 metal tablespoons
1 laboratory balance
1 metal tray to hold hot candies (up to ~ 175ºC/350ºF)
1 laboratory of good quality thermometer that reads up to ~ 205ºC or 400ºF
5 pounds of granulated cane sugar
16 oz. bottle of corn syrup
Drinking water
20 molds for casting. (The metal containers from Tea Light candles work well or small cookie cutters)
4 eight oz. glasses
Crystal candy, available in clumps of large, colorless crystals
Experiment A- Pure sugar.
1. Place molds on metal tray.
2. Put 410 g sugar in the pan and gradually heat on hotplate or electric stovetop at low-medium temperature. Insert thermometer and monitor the temperature of sugar.
Stir sugar with spoon in order to maintain uniform temperature throughout. Note: keep thermometer bulb in the middle of sugar, but away from the bottom of the pan.
3. Continue to stir at a rate that best mixes solid and molten parts. Continue heating and stirring until all the sugar has melted. The stirring speed should be such that solid and molten parts mix together. Record the temperature at which the sugar melts.
4. At this point, stop stirring and prevent the temperature from increasing. Temperature increase would cause excessive browning and the formation of bubbles, symptoms of the decomposition of sugar.
5. Put one tablespoon of molten sugar in mold (sample #A1) and three tablespoons in a different mold (sample #A2). Note: molds can be easily marked and kept track of with permanent marker.
6. Record the physical appearance of the samples as they cool to room temperature. Make observations regarding transparency, presence of small white crystals and/or bubbles, and solid or liquid state.
7. A fiber draw can be created by slowly pull a spoon out of the melted sugar. Record a prediction for which temperature the fiber draw will be at the height of its ability.
8. Turn the hotplate off. Make several fiber draws, all the while noting the temperature. Continue this process, as the temperature decreases and the sugar becomes more solid, until a fiber draw is no longer possible. Note the temperature at which the fiber draw reached its maximum ability.
9. Compare the appearance of samples #A1 and #A2 with that of crystal candy that is also made of pure sugar.
Experiment B- Sugar and water modifier.
1. Put 410 g sugar and 100 g water in the pan and begin heating while stirring the melt. Monitor increasing temperature as sugar dissolves. Record the temperature at which all the sugar dissolves.
2. Continue to heat and stir. Record the temperature at which the syrup begins to boil.
3. Cast candy from the syrup (sample #B1). Record the physical appearance of the samples as they cool to room temperature. Make observations regarding transparency, presence of small white crystals and/or bubbles, solid or liquid state. If the sample remains fluid once it has reached room temperature, note its relative viscosity.
4. Continue to stir and boil the remaining syrup until the temperature increases by 5. °C (or 10 °F) If solid sugar deposits on sides, scrape and stir it into the liquid. Cast candy from this more concentrated syrup (sample #B2). Make a note of the physical appearance as in step three of experiment B.
5. Repeat step 4, casting a new candy for each 5 °C (or 10 °F) increment in temperature (sample #B3, #B4, … etc.). Continue until the temperature reaches 170 °C (338 °F).
Be sure to use a clean spoon to cast each new sample.
Experiment B(a)- Sugar and water; without stirring.
1. Repeat all the steps of Experiment B, except this time do not stir the solution after the sugar has settled at the bottom of the pan (at 200 F). Try to cast the samples (#B1(a), #B2(a), #B3(a),… etc.) when the melt is at the same temperature as in Experiment B.
2. Record the changes in samples as they cool to room temperature, making special note of any differences compared to the corresponding B samples.
Experiment C- Sugar, corn syrup and water.
1. Repeat Experiment B(a) using 240 g corn syrup, 410 g sugar and 100 g water in a clean pan.
Testing: Effect of processing conditions on the properties of candies.
Hardness or Chewy character. The samples should have a wide range of hardness from brittle solid to a watery liquid. To make a comparison of this property, use a paper clip. Open up a paper clip to have one sharp end and keep the rest bent. For the solid samples, insert the sharp end with consistent force into each sample and compare the size of the dents created. For liquid samples, use the bent end of the paper clip. Dip it into the liquid and take it out, noting the relative force needed.
Durability in water. For one temperature, select a sample from each of the A, B, B(a) and C experiments (i.e. the cast from the melt at 150 °C or 302 °F). Weigh (still in mold) on laboratory balance and place them in separate 8-oz. glasses with 200 g tap water. (Note: all the water should be at the same temperature). Drain the water out after 1 hour. During this time, avoid disturbing the sample and water. Take the samples out, dry and weigh them again. Calculate the respective weight loss due to the water dissolving the sample. Each sample has equal surface area exposure to the water, thus making the weight loss inversely proportional to the durability; the greater the weight loss, the lower the sample’s durability.
Hint for recording information onto a table: When possible, assign relative grades of 1 through 5 to non-quantative information. For example, in a column for transparency, write 1 for an opaque and 5 for a completely transparent sample.